This article is based on the findings in the report, Understanding the Impacts of Industry 4.0 on Manufacturing Organizations and Workers, prepared for the Smart Factory Institute and written by Chris Cunningham, PhD, UC Foundation Professor of Psychology, and Scott Meyers, Graduate Assistant, Psychology Department & Smart Factory Institute, from the Industrial and Organizational Psychology Department at the University of Tennessee at Chattanooga.

The many new and advanced technologies associated with Industry 4.0, including the shift from repetitive and physical to more strategic and intellectual forms of manufacturing work will affect workers’ experiences in manufacturing organizations. The technologies at the core of Industry 4.0 are most likely to benefit manufacturing as well as supply chain and retail operations (Wong, 2021), but given the centrality of these industries to the global economy, the impacts of Industry 4.0 on workers’ experiences will be broad. Some of these effects will likely be negative, but others will be positive.
Among the potential and anticipated negative effects of Industry 4.0 on the worker experience is a new round of worker anxiety that often accompanies technological progress. In previous periods of technological advancement, serious concerns arose regarding the risk that machine automation might replace labor all together and thus constitute a form of moral wrong by dehumanizing workers (Mokyr et al., 2015). More recently, these types of concerns have revolved around fears that advanced technologies associated with Industry 4.0 might result in the elimination of many work roles in which manufacturing workers are often employed. This so-called “automation anxiety” has been an increasing concern for workers; in 2017, the Pew Center reported that 72% of Americans were worried about the job impacts of automation (Litan, 2018). Worker perceptions are important to understand, especially when they influence worker attitudes and ultimately behaviors on the job. Some of this worker anxiety is warranted, given that Industry 4.0 automation and new technology developments will put specific types of manufacturing jobs and tasks at risk. A PwC study estimated 38% of U.S. jobs could potentially be at high risk of automation by 2030. In comparison to other countries, this risk was 35% in Germany, 30% in the UK, and 21% in Japan. Manufacturing was the second highest industry at risk for automation at 46%; transportation and storage had the highest risk with 56%. (Statista, 2021). In comparison, sectors like health and social work had much lower risk with 17%. Resulting from these automation-induced shifts in the design of work, low skilled workers involving repetitive, administrative, menial, and pattern-base tasks in manufacturing will experience a significant threat of job loss as Industry 4.0 technology progresses (Shet & Pereira, 2021). This will be even more true for workers who do not wish to take on additional responsibilities or decision-making authority that come with more strategically oriented and technologically rich manufacturing roles.
In many ways, the technological progress made in the Industry 3.0 and now 4.0 periods are leading to long-term benefits such as new forms of employment and economic growth. It is important to emphasize that the adoption of Industry 4.0 is not simply or even predominantly a “jobs killer” moment for manufacturing. While automation will reduce the need for types of work that is less complex and more routine, these same technologies will also create more highly skilled and strategic job opportunities that may present more complex and diversified worker requirements (Shet & Pereira, 2021). The BCG projects that for every six jobs that are automated, one new or additional job is required to develop and run the associated technology (Strack et al., 2021). Although the future is unknown, a potentially helpful illustration of what is expected now as a result of Industry 4.0 may be provided by looking back at what happened following the introduction of personal computers: An estimated 3.5 million jobs were lost, but another 19.2 million jobs were created, in America alone (Wong, 2021).

Thus, although there is great public distress over technology automating and taking jobs away from human workers, at a high level, more automation increases the production rates of manufacturers. Industry 4.0 brings new efficiency and overall increased manufacturing productivity. This increase in production creates new job positions and workforce opportunities (Pejic-Bach et al., 2020; Shet & Pereira, 2021). From technology and increased automation, will emerge new business, new services/products, new markets, and new job opportunities. This, in turn, is likely to lead to more hiring as more people are needed to meet the overall increased production demands (Dixon et al., 2021; Knowledge at Wharton, 2021) and generally more stability within the manufacturing sector as more organizations adopt and benefit from Industry 4.0 advancements.
General Electric projects the industrial IoT alone will add more to the world economy than every major country except for the U.S. and China by 2030. This would result in more employment and higher incomes (Statista, 2021). Other reports evidence the robust improvement in global employment and increases in both number of employees and hours worked (Sima et al., 2020). Within all industries, the proportion of new workers to total employment is projected to increase 11% while the proportion of job loss to total employment is projected to decrease by 10% by 2022 (World Economic Forum, 2021). The pandemic has also increased the rate of adoption of new technologies and innovations. Without question, the new technologies associated with Industry 4.0 will greatly change the employment landscape. Automation is not projected to result in a loss of jobs, but rather a shift in roles (Statista, 2021). Regardless, these changes in jobs and workforce requirements create a potentially large economic disruption that will impact manufacturing workers, their organizations, and associated policies and practices (Strack et al., 2021).
There are many other potential benefits to be anticipated as outgrowths of Industry 4.0, particularly associated with new job opportunities and ways of working. As one example, the major increase in automation and human-machine collaborative technology opens new opportunities for inclusion of disabled workers who may not have been able to work in past manufacturing contexts that mainly or solely required workers to meet physical work demands (Mark et al. 2019; Shet & Pereira, 2021). Industry 4.0 brings new worker assistance technologies in the form of sensorial aid systems, physical aid systems, and cognitive aid systems to support disabled workers in manufacturing (Mark et al., 2019). Furthermore, as the more physical and repetitive job tasks become automated, new more complex positions that require greater critical thinking, strategy, and technical skills will become more relevant, opening additional pathways for physically disabled workers to shine (Flores et al., 2020, Shet & Pereira, 2021).
These changes towards more complex work design also hold the potential to benefit the broader manufacturing workforce. Digging a bit further into this matter of job complexity, it is important to note that high job complexity involves tasks that are multi-faceted, mentally challenging, and require complex skill (Campion, 1988). The Job Characteristics Model of worker motivation and performance illustrates how jobs with specific core dimensions including skill variety, task identify, task significance, autonomy, and job feedback create specific and positive psychological states in workers which ultimately lead to increased motivation (Hackman, 1980; Hackman & Oldham, 1975). One of these critical psychological states includes experiencing meaningfulness of the work such as the extent to which workers feel their job is valuable (Chung-Yan, 2010). High job complexity has been associated with positive attitudinal and behavioral outcomes such as job satisfaction, job performance, organizational commitment, job enrichment, internal motivation, and perceived opportunities at work (Gould, 1979; Humphrey et al., 2007; Schleicher et al., 2004; Zacher & Frese, 2011). Worker job satisfaction is particularly important as an attitude to monitor within organizations that are adapting or changing to leverage Industry 4.0 technologies more fully. This job-related attitude is associated with workers’ perceptions about their overall job and specific job aspects (Spector, 1997). The introduction of new jobs and new technologies, as well as changes in work design such as increased connectivity including communication and collaboration among workers may be more strongly aligned with worker preferences, leading to higher job satisfaction (Soldo, 2021). It is possible that these types of positive effects on worker attitudes may support efforts to attract and retain skilled workers.

Extending from this very large and robust research evidence base, it is very likely that the more complex jobs and job tasks associated with Industry 4.0 can benefit workers in many ways, as long as workers have opportunities to develop requisite and corresponding new knowledge, skills, abilities, and other characteristics (KSAO) and competencies they need to effectively respond to changing work demands. In addition to generally increasing workers’ human capital and value, increased job complexity and corresponding training and development make it possible to increase worker job satisfaction with manufacturing work via mechanisms such as increased worker sense of meaning and purpose associated with their jobs. For example, the strategic nature of many Industry 4.0 manufacturing jobs involves meeting complex demands of a specific issue or problem within the production system. This task could lead to greater worker perceptions of meaning and accomplishment compared to prior manufacturing work involving simpler repetitive tasks to meet a production goal. Similarly, the IoT-mediated possibility for manufacturing organizations to respond to actual customer needs opens up opportunities for manufacturing workers to work directly to address the needs of others, rather than simply producing products following a set schedule created for general consumer demands. This component provides greater task significance, another job design characteristic contributing to positive worker outcomes (Hackman & Oldham, 1975)
It should be noted that these mentioned job complexity relationships are in themselves complex and other factors such as worker’s individual differences could alter worker experiences. For example, high job complexity was found to be most associated with positive outcomes such as satisfaction and psychological well-being when job autonomy was also high (Chung-Yan, 2010). Additionally, past research has indicated curvilinear effects of job characteristics such as complexity on performance where too little or too much may actually be associated with negative impacts. Industry 4.0 and effects on worker experience is still a relatively new area of study. Further research will be needed to understand exactly how manufacturing workers experience and respond to the elements of Industry 4.0. A particular area needing additional study is on the relationship between Industry 4.0 and worker health, safety, and well-being (Waldmann et al., 2020). Once manufacturing organizations have trained and recruited all the smart workers they need, they will ultimately have to make sure these workers are kept safe and healthy.
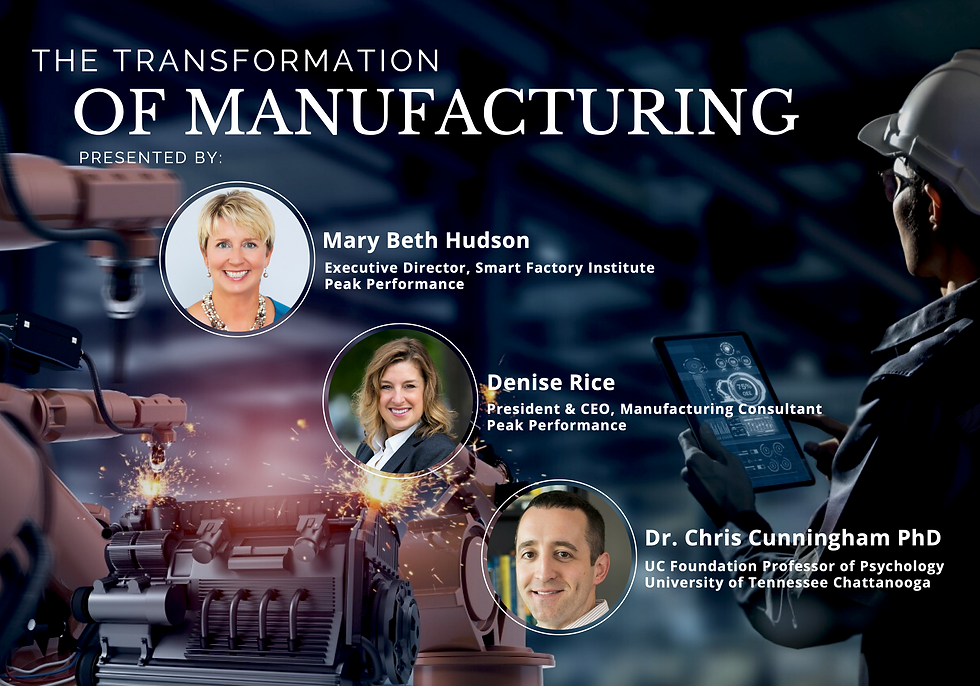
Join us LIVE, as we explore the current manufacturing industry and the challenges and opportunities it faces in the midst of the adoption of Industry 4.0. The Transformation of Manufacturing, 3-stop tour across the state of Tennessee, will wrap up tomorrow with its final stop in Smyrna, TN.
February 16, 2022 | 7:30am - 8:30am (CT)/8:30 - 9:30am (ET)
Location: TCAT Smyrna/Nissan Training Center, 663 Ken Pilkerton Dr., Smyrna, TN 37167
In-Person & Virtual Attendance Options Available
Sessions are free to attend, registration is required.
This tour is based on the findings in the report, Understanding the Impacts of Industry 4.0 on Manufacturing Organizations and Workers, prepared for the Smart Factory Institute and written by Chris Cunningham, PhD and Scott Meyers from the Industrial and Organizational Psychology Department at the University of Tennessee at Chattanooga. Get access to this full report by clicking here.
Comentarios